5517 Peripheral Equipment
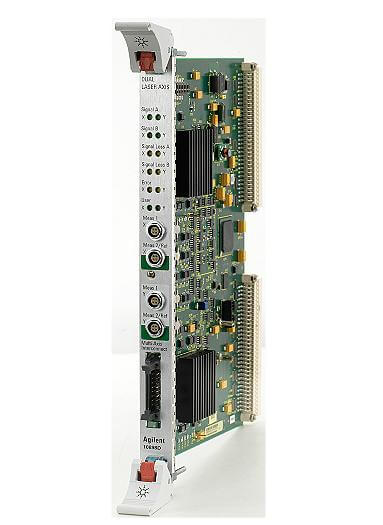
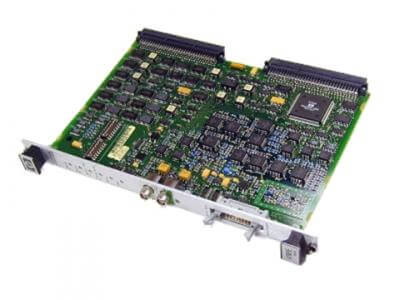
Laser Electronic Axis Card Series and Axis Card Fiber Optic Signal Transmission Cable
Utilizing electronic axis cards, signals acquired at the receiver end are transformed into readable data. In response to various user needs, the current highest resolution can reach up to 0.15nm, with a division factor of up to 1024 times. This breakthrough surpasses the previous limitations on stage movement speed and reduces noise, providing superior applications such as repeated positioning accuracy and precision in IC manufacturing equipment. Its high data conversion rate satisfies the requirements of high-bandwidth and high-performance closed-loop systems.

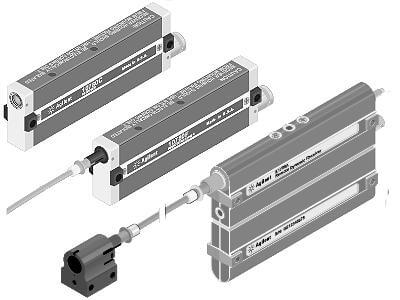
Laser Receiver
The receiver is used for each measurement axis to capture laser beams divided through the multi-axis setup. It measures changes in displacement between machine operations. Keysight (Agilent) receivers have evolved from integrated mirror assemblies to transmitting signals directly to VME electronic axis cards via fiber optics. This flexibility enables users to make precise adjustments to positioning. For instance, with the N1225A model, multiple N1225A boards connected together can achieve position measurement for up to 31 axes. When combined with Agilent laser heads, fiber optics, and optical configurations, users can tailor a precise positioning system to meet stringent application requirements.

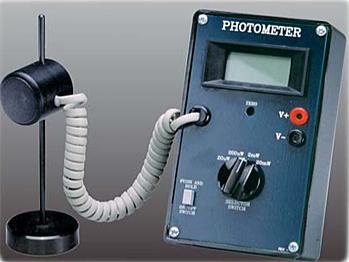
Laser Power Meter
Despite Keysight lasers having an operational lifespan exceeding 50,000 hours in industrial-grade usage, laser power and frequency may experience degradation over prolonged usage. Additionally, due to variations in optical path designs across different machines, laser light undergoes multiple splittings. By the time it reaches the light receiver, its power might have declined to below the receiver’s minimum detection threshold. To diagnose aging or weakening of the laser tube, it is recommended to invest in a laser intensity detection meter (Laser power meter). This meter detects any inadequacy in laser intensity, helping to determine whether a laser head replacement is necessary during machine maintenance. This proactive step prevents machine downtime caused by laser intensity degradation, thus minimizing production losses.